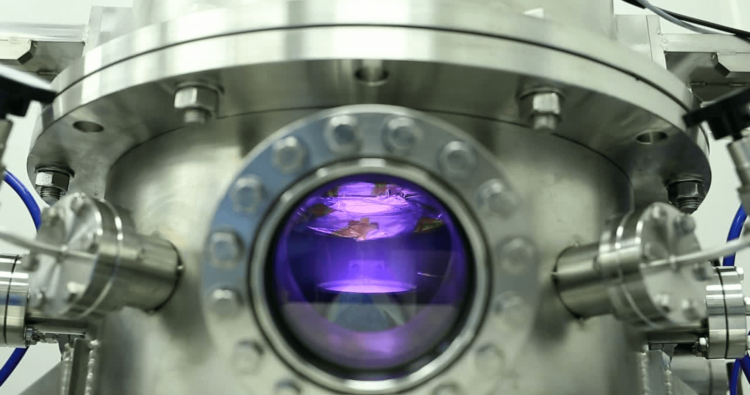
Nozzle coating and its contribution to 3D printing industry
- 24. 2. 2022
The issue of coatings is a frequently mentioned topic. Many may argue that with current technology it is not possible to effectively coat the bottlenecks and thus their use becomes meaningless. In the case of nozzles, we are talking about the channel (pinhole) where the printed material is extruded, plus the part of the constriction - from the inner cone to the nozzle mouth where the material is extruded out.
With this article, we would like to refute this and bring you more about the coating technology.
PVD, physical vapour deposition, is a technology where an arc (plasma) is used to deposit a very thin layer (on the order of units of um) of a target of a suitable chemical composition onto a coated object. There are many types of coatings and they differ in deposition temperature (so-called deposition temperature), temperature resistance, hardness, slip resistance, etc.
Although it only reaches a relatively small depth from a physical point of view, it partially protects the interior, but especially the tip which has the greatest influence on the appearance and parameters of the print. Another nice feature is the reduction of material sticking to the nozzle, so maintenance is significantly easier.
Probably the best known of the PVD coatings is DLC "diamond-like-carbon". This is a carbon-based coating where, during deposition, a smaller or larger proportion of the crystalline lattice of carbon is changed to a diamond-like type, the rest being in the form of graphite. This ratio will determine the hardness and slip resistance of the coating. This type of coating is what the giant E3D, or ObXidian nozzles with E3DLC™ coating, comes up with.
We too have used this coating in the past, but it has its pitfalls. The coating is applied at a lower temperature (deposition on the order of 250-350°C) and is, therefore, easier to apply. Its use is indicated up to about 450°C, but in practice, it appears that longer exposure to temperatures above 250-300°C changes the lattice and the diamond becomes graphite. The coating thus loses its properties and degrades overall. For these objective reasons, we have completely moved away from DLC type coatings and it is a happy surprise to us, that other manufacturers are just start discovering this solution.
Despite the satisfaction of the vast majority of our customers, we are not stopping our development and introducing an even more suitable and reliable solution for 3D printing overall. Over the past year, we have analyzed and tested a number of coatings with different chemical compositions.
Now we would like to offer nozzles with a new generation of rigid, slippery and reliable coating that is not DLC-based and does not degrade its crystalline lattice. At first glance, they don't look much different from the previous ones, but the opposite is true. If you have our previous generation nozzle or the new one, you can tell by the following picture. The nozzles are now completely black, matte with a very rigid coating and signed with our logo and nozzle diameter.
The new coating provides its full properties over the entire temperature spectrum from 0 to 550 °C and shows increased abrasion resistance, especially when printing Nylon-CF etc.
Of course, the nozzle material itself also has a great influence on the properties. Our nozzles are made of a very hard copper alloy due to the balanced ratio of resistance and thermal conductivity.
Now we are also preparing a novelty for connoisseurs, where one of the hardest alloys available on the market will be used, which also has self-lubricating properties, and this nozzle will also use a coating, in addition to the most advanced technology that has limitless potential.