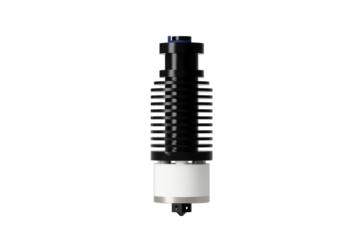
Need help? info@protoprint3dp.com
RAPTOR is the result of our strongest efforts and years of research. This hot-end connects the best possible features and properties in order to deliver the best possible result.
Versatility. All-metal design. Super-easy maintenance. Heating up to 500°C. Unique patented heat-break. Reduced power consumption. Precise copper nozzle with a special surface coating. Compatible with the major known 3D printers such as a Prusa and others.
Whole nozzle consists of Copper part (nozzle itself), stainless steel alloy tube with thickness ~0.15mm (as a heatbreak), and high-thermal conductive Aluminium. This combination significantly (more than 3x than typical threaded heatbreaks) limiting thermal transfers to heatsink and preventing material leakage. Patent pending!
Surface coating grants perfect wear-resistance and material sliding. Melt zone is one coherent piece 13,5mm long!
Maintenance has never been easier! Now you can easily remove the nozzle without pre-heating the whole hot-end! Changing in seconds, at a room temperature, with no burn risks.
Melted and baked material leftovers on the nozzle removed smoothly in a seconds. This is a feature of the surface coating. Easy, fast and safe.
Maximum performance, versatility and durability without compromise. Unique patented Heat Element (core) with Zirconium Oxide (ZrO2) shielding and maintenance-less 60W ceramic heating ring can reach up to 500 °C while radiating very low waste heat to outer space.
Extended melt zone secure more melted material and possibility to speed-up the printing as per your skills.
Thanks to the core design, the thermocouple probe is located directly next to the heating ring. The result is maximum preciseness in a temperature sensing & control leading to the stable printing process.
We use only the top quality high-temp thermocouples with glass fibre insulation and Molex Microfit 3.0 connector.
Unique circular shape ceramic heating element grants absolutely uniform melting and thus better overall printing results.
Thanks to the smart design of RAPTOR's core and absence of the standard heating cartridge we are able to reduce electricity consumption while achieving better printing results.
Weight is almost 20% reduced than the typical most used hot-ends, which leads to higher speeds of printing and reduce stress to key components on the 3D printer. Hotend without wires weighs 40 grams, with wires 45 grams.
Maximum performance with lower weight and less power demand.
3D printing in enclosed chamber unlock the access not only to the better overall control of the printing process. Noise and heat loss is reduced. Best possible printing quality is achieved thanks to stable temperature and very low heat fluctuations.
With water cooling you can handle the most demading materials and achieve great results.
Hotend's endurance was tested and evaluated with several complex simulations. We use special ceramic heaters with estimated life of 10.000 hrs. Every used material is designed to fulfill the goal of whole Hotend - to deliver the best result during 3D printing.
We simulated thermal transfer of crucial components and measured air flow trajectory and velocity streamline to verify the thermal behavior.
During the development, RAPTOR was repeatedly consulted and subsequently simulated by researchers in the research center RICE - Research and Innovation Center for Electrical Engineering, which is part of the Faculty of Electrical Engineering of the University of West Bohemia in Pilsen.
The design of the hotend was fine-tuned based on the analysis summarized in the research report. The cooperation with the center is intensive - we are currently working together on research and simulations of the new Direct-drive extruder Thunderhead and other projects.